Roofers Helena MT are skilled professionals who install, repair, and maintain the roofs of various types of buildings. They work closely with architects and builders to ensure that construction is completed according to building codes and regulations.
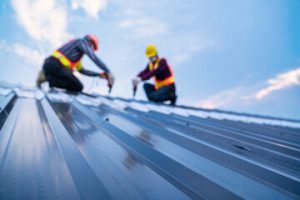
The job requires significant physical stamina and balance, as well as the ability to work at heights. It also requires knowledge of a variety of roofing materials.
Roofers install, repair, and replace roofs on homes and buildings. They use various roofing materials and follow construction plans and specifications. They may also inspect a building’s interior and exterior to determine how best to proceed with the roofing work. They are also responsible for installing supporting accessories, such as trusses and beams. They must be able to work on ladders for extended periods and have good attention to detail.
A high school diploma is usually required to become a roofer, and on-the-job training is common. Some roofers learn the trade through a formal apprenticeship program, which can take between three and five years to complete. These programs include hands-on training and classroom instruction. In addition to learning the basics of roofing, apprentices must also pass a background check and drug test.
Once they have completed an apprenticeship, roofers can choose to become a journey worker or advance to a position as a foreman. In both positions, roofers are responsible for supervising other workers and ensuring that all work meets quality standards. They must also be able to read blueprints and technical drawings and be able to perform basic math. Additionally, roofers must be able to operate hand and power tools and climb up scaffolding for long periods of time.
Some roofers specialize in commercial projects, while others focus on residential construction. A commercial roofer will often have a different skill set than a residential roofer, as commercial projects have more complex designs and require specialized materials. These professionals will also be able to offer advice on a variety of topics, such as energy efficiency and sustainable building practices.
In addition to being a physically demanding job, roofing is also highly dangerous. In order to be successful in this field, one must have a strong work ethic and the ability to follow safety standards. A strong knowledge of building codes is important, as are good organizational skills. It is also helpful to have a strong eye for details and a willingness to work in a variety of weather conditions. A successful roofer will also have a good understanding of the building industry and its financial aspects.
Education and training requirements
Roofers play a critical role in construction, protecting buildings from the elements and maintaining structural integrity. They typically don’t need a college degree and enter the industry through apprenticeships or on-the-job training. They also must be able to work at heights and have strong manual dexterity. This career is not for everyone, however, as it can be dangerous and physically demanding. In addition, it requires continuing education and training to stay abreast of new materials and techniques.
Most roofers learn the trade informally by working as helpers for experienced professionals. During this time, they take safety classes and learn the basics of removing, cutting, and installing roofing materials. In some areas, roofers may be required to pass a state or regional certification exam to qualify for a roofing license. In general, roofers should be familiar with all types of residential and commercial roofing materials.
Some roofers are employed by roofing companies, while others run their own businesses. Those who are self-employed must have excellent business skills to manage their finances and customers. It is also important for roofers to have good problem-solving skills, as they often encounter unexpected challenges on the job site. They must be able to assess weather conditions and structural issues quickly and find effective solutions.
Many unions and contractor organizations offer apprenticeship programs for prospective roofers. These programs combine on-the-job training with classroom instruction, usually for a set number of hours per week. The length of an apprenticeship program varies depending on the location and local regulations. Individuals with previous construction or roofing experience can progress through the apprenticeship process more quickly.
After gaining sufficient experience, roofers can advance to supervisory positions or start their own roofing company. Some roofers choose to become specialists in particular roofing disciplines, such as shingle or metal roofing. They also can obtain additional certifications, such as a roofing foreman’s certificate.
Applicants for roofing jobs should have a high school diploma or equivalent, good physical condition, and the ability to perform physically demanding tasks at heights. They must be able to follow instructions and work as part of a team. They should also have a strong attention to detail and good communication skills.
Work environment
Roofers construct, cover, and repair the roofs of commercial and industrial buildings, residential homes, and other structures. They use a variety of roofing materials to ensure that these roofs are watertight and weatherproof. They also install insulation and vapor barriers to improve energy efficiency. In addition, they may install gutters and downspouts to prevent water damage. Roofers typically work at heights and in a variety of weather conditions, but they follow safety guidelines to ensure their work meets quality standards.
Roofer jobs require workers to be physically fit and mentally engaged. This career is often challenging, and workers must be prepared to lift heavy loads and continuously knell or bend while working on the roof. Workers must also be aware of the potential hazards associated with working on a roof, including falls and exposure to chemicals and electrical hazards. In addition, roofers must wear appropriate safety equipment.
Roofing is an in-demand skill, and there are many opportunities for people who want to work as roofers. These include specialized projects, such as green or solar roofs, and new construction. This career can be rewarding because it allows workers to directly impact the safety and comfort of families. Moreover, roofers can help with disaster recovery efforts by repairing damaged houses.
While there are many different ways to become a roofer, the best way to start is by enrolling in a registered apprenticeship program. These programs offer a comprehensive education at no cost through a combination of classroom instruction and on-the-job training. Upon completion of the apprenticeship, workers can earn competitive wages and move into supervisory roles.
The work environment for roofers can be dangerous, especially during summer. The intense heat can cause symptoms of dehydration or heat exhaustion. Workers must be able to recognize these symptoms and seek medical attention as soon as possible. This is particularly important because falling from a roof is one of the most common causes of workplace injuries. These workers are also at risk of getting burns from tar or other roofing chemicals. Fortunately, adherence to safety rules can decrease the number of accidents.
Salary
Roofers are skilled tradespeople who install, repair, and replace roofs on residential and commercial buildings. They use a wide variety of materials, including shingles, tiles, slates, and hot bitumen. Some are members of a union, which can increase their wages. Typically, the more experienced a roofer is, the higher their salary will be. In addition to their technical skills, they also need good judgment and communication skills to work with architects and other construction workers.
Roofer salaries can vary greatly depending on a number of factors, such as the job location and state, the average hourly wage, and their level of experience. It is important to know how much the average roofer makes in your area before starting a career in this field.
In the United States, roofers can expect to make an average of $42,700 a year. However, the exact amount depends on a number of factors, such as a region’s cost of living and the demand for roofing professionals. These figures are provided by the Bureau of Labor Statistics.
Those who wish to become roofers should have no fear of heights and be physically fit. They should also enjoy working with their hands and have excellent hand-eye coordination. A high school diploma is not a prerequisite for this position, but a college degree is preferred.
Most roofers learn their trade through on-the-job training or an apprenticeship. Beginners start as helpers, performing simple tasks such as carrying equipment and setting up scaffolding. Later, they can learn how to perform more complex tasks and gain the skills necessary to build and repair roofs.
Roofers can choose to work for a general contractor or a roofing company. They can also choose to specialize in a particular type of roofing system. Once they have a sufficient level of experience, they can advance to supervisory positions or serve as estimators. Eventually, they can even go into business for themselves as independent roofing contractors.
In the summer, roofing companies across the country can expect to see an influx of customer requests. In order to keep up with the workload, these businesses should consider using field service management software to streamline their operations. This software can help you improve employee productivity and efficiency, which is especially important during busy season.